Electrophoretic Coated Brake Rotors
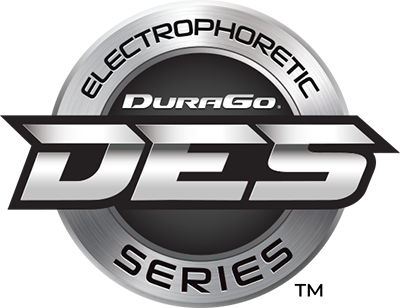
(DES) Series
Electrophoretic Series Coated Brake Rotors offer dynamic performance with the utmost in corrosion resistance. They are superior from the inside out due to a submerged coating process that ensures 100% coating coverage of the inner vanes and all exposed non-braking surfaces.
During the Electrophoretic process, rotors are fully immersed, resin particles are suspended within a liquid medium and have a charge placed upon them. Under a charged current, the coating particles migrate to the rotor and are deposited onto all exposed surfaces, resulting in a highly corrosive resistant and durable coating.
After the rotor is coated, it is thoroughly rinsed and baked to harden the coating. Once the coating is cured, all of the braking surfaces are machine finished.
- Premium Core Technology Allows for tighter tolerances and cleaner castings. With this process, non-machined areas of the rotors are more detailed.
- Machine Balanced for smooth braking.
- Multiple Vane configurations for heat dissipation.
- Non-Directional Swirl Finish promotes brake pad bedding and eliminates the need for machining prior to installation.
- Electrophoretic Coating Utilizes a form of electroplating to apply a rust resistant coating directly to the rotor resulting in a highly corrosion-resistant finish.
- In the electrophoretic process an electric current is run through a rotor that is submerged in an electrophoretic coating emulsion. The energized process promotes the coating to adhere like a magnet to both the inside (vane area) and outside of the rotor.
- Engineered To Meet All Requirements Of Fit, Form And Function
- Multi-Stage Q.C. Process To Ensure Parts Meet Dimensional And Weight Specifications
- Non-Directional Finish For Improved Brake Pad Bedding
- Manufactured In IATF 16949:2016 Certified Facilities
- Detailed Cores For Tighter Tolerances And Cleaner Castings
- SAE J431 Metallurgy
- Computerized Machining For Tight Tolerance Controls
- Braking Surfaces Uncoated For Optimal Brake Pad Bedding
- Dynamic Black Finish Complements Vehicles With Open Wheel Designs
- Rust Resistant Coating Protects Against Corrosion
- Multi-Stage Quality Control Coating Process Ensure Proper Application
- Coated Hat And Edge For General Corrosion Protection
- Submerged Coating Process Ensures 100% Coating Of Inner Vanes And All Exposed Non-Braking Surfaces
- Fully Coated Inside & Out – Inner Vanes And All Exposed Non-Braking Surfaces
- RoHS Compliant Coating (Meets Strict Environmental Standards)
- 300+ Hour Salt Spray Protection
- Superior Salt Protection – Tested Per (ASTM B-117/ISO 9227)
- Eye Catching Tri-Lingual Graphic Box With Detailed Features And Benefits
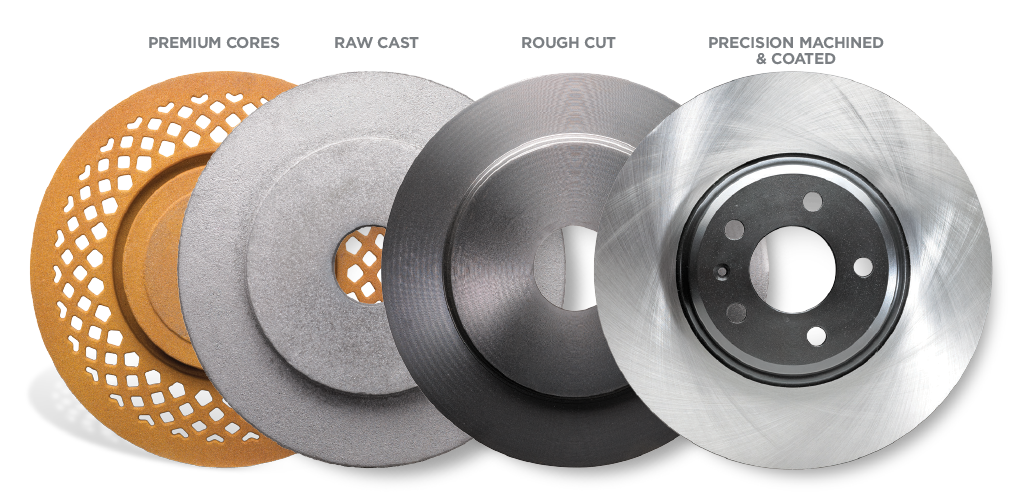
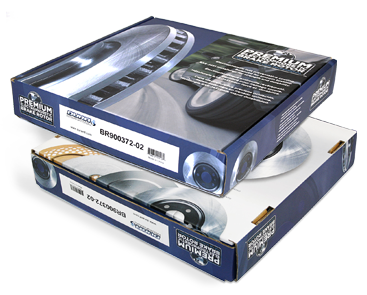
Electrophoretic Process
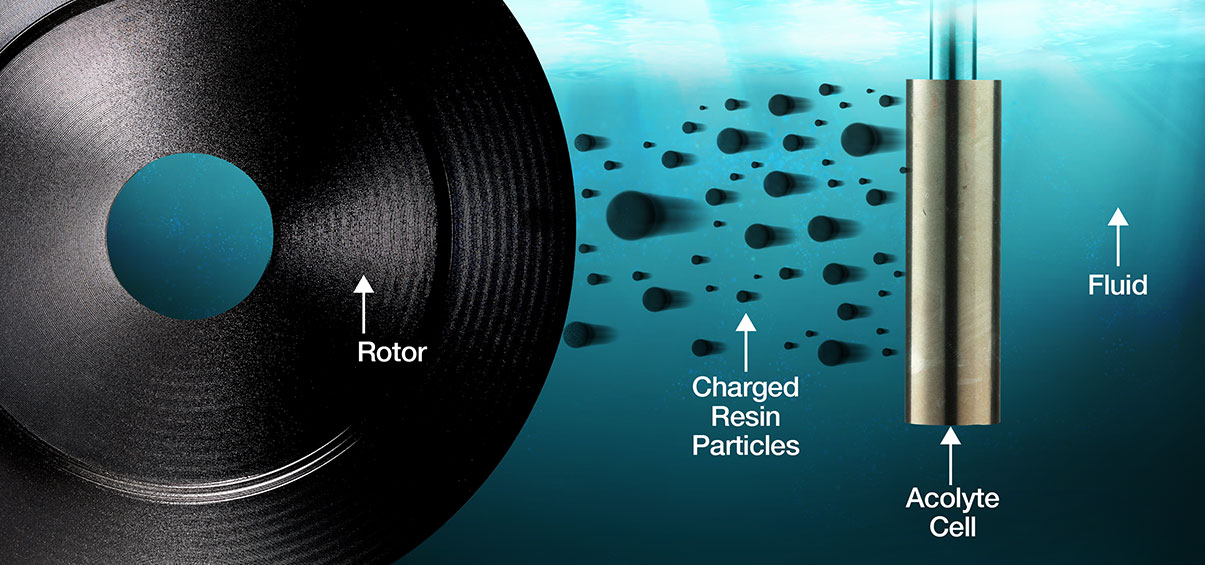
During the Electrophoretic process, rotors are fully immersed, resin particles are suspended within a liquid medium and have a charge placed upon them. Under a charged current, the coating particles migrate to the rotor and are deposited onto all exposed surfaces, resulting in a highly corrosive resistant and durable coating.
After the rotor is coated, it is thoroughly rinsed and baked to harden the coating. Once the coating is cured, all of the braking surfaces are machine finished.
Superior Braking Performance
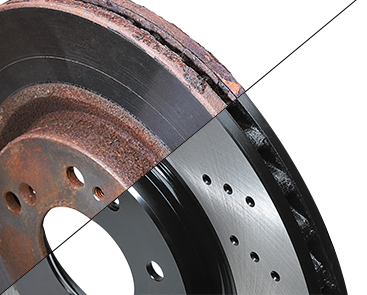
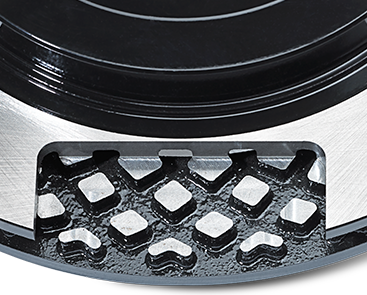
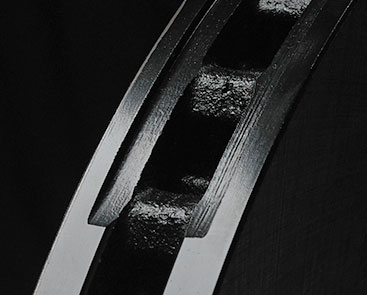
Electrophoretic coated areas of the rotor have the utmost corrosion resistance and superior esthetics. The Electrophoretic coating is bonded to the rotor for increased protection from rust and corrosion.
Advanced Coating for Advanced Protection
The DuraGo® Electrophoretic process deposits the advanced coating onto all exposed surfaces, protecting the rotor both inside and out.
DuraGo® Electrophoretic Rotors are 100% mill balanced for optimum braking performance.